Industrial shredders play a crucial role across various sectors by handling material reduction needs efficiently and sustainably. However, choosing the right shredder can be challenging, particularly when it comes to understanding the pricing structure. Designed to demystify this topic, this article sheds light on the factors influencing the cost of industrial shredders and how they bring value to your operations.
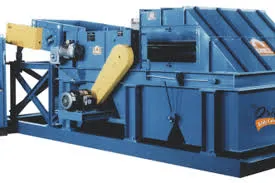
One of the primary aspects influencing industrial shredder price is the type of shredder. Common types include single shaft, double shaft, and quad shaft shredders, each designed for specific materials and applications. Single shaft shredders often come at a lower cost but are best suited for smaller and less demanding tasks. For operations requiring greater robustness and versatility, double shaft or quad shaft models are ideal, albeit they tend to be priced higher due to their enhanced capabilities and durability.
Material composition and durability are key determinants of cost. High-quality industrial shredders are fabricated using durable materials such as hardened steel. This ensures longevity and reduces maintenance costs over time, reflecting a higher initial price point but benefiting the user with a longer service life and fewer interruptions in operations. Investing in a sturdy machine translates to fewer breakdowns and superior throughput efficiency, which, over time, justifies the upfront investment.
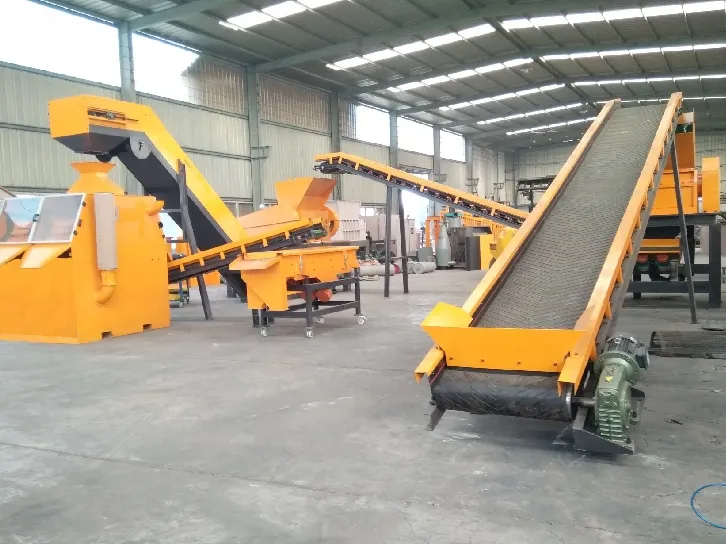
The size and throughput capacity of a shredder also directly impact its price. Industrial operations vary widely in scale; therefore, choosing a shredder that aligns with your material processing volume is crucial. High throughput machines designed for processing large volumes at once are generally more expensive, as they require robust motors and sophisticated designs to ensure efficiency and reliability.
industrial shredder price
Another variable affecting price is the level of technology integrated into the shredder. State-of-the-art shredders equipped with advanced features like automated controls, programmable logic controllers, and safety mechanisms can increase productivity and safety, but these features also carry a premium. The investment in technology often pays off through enhanced precision, ease of use, and adaptability to varied tasks, which can enhance overall operational productivity.
Beyond machinery specifications, geographical location and market dynamics play roles in pricing. Costs can vary significantly based on the manufacturer’s origin and the economic conditions of the customer’s region. For instance, import tariffs, shipping fees, and currency exchange rates can contribute to cost variability. In addition, industry demand-supply conditions can affect prices – during periods of higher demand, costs might surge, impacting your investment decisions.
When considering the price, one must also account for the long-term benefits of owning an industrial shredder. These machines not only facilitate efficient waste management and material recycling, reducing disposal costs, but can also contribute to revenue streams through the sale of recycled materials. This dual financial impact can render a higher-priced model economically advantageous over its lifespan, creating a significant return on investment.
In conclusion, understanding the industrial shredder market is imperative for making informed purchasing decisions. The initial cost of a shredder is multifaceted, influenced by the shredder type, material durability, size, technological sophistication, and market variables. Evaluating these aspects, along with long-term operational benefits, enables businesses to select the ideal shredder that meets their operational needs within their budgetary constraints. Through informed decision-making, companies can achieve both cost efficiency and operational excellence, positioning themselves advantageously in their respective markets.