At the heart of modern recycling plants lies a complex, meticulous process dedicated to sorting metals, transforming what many perceive as waste into valuable resources. The journey of metals through these plants is a testament to the innovative blend of technology and environmental stewardship.
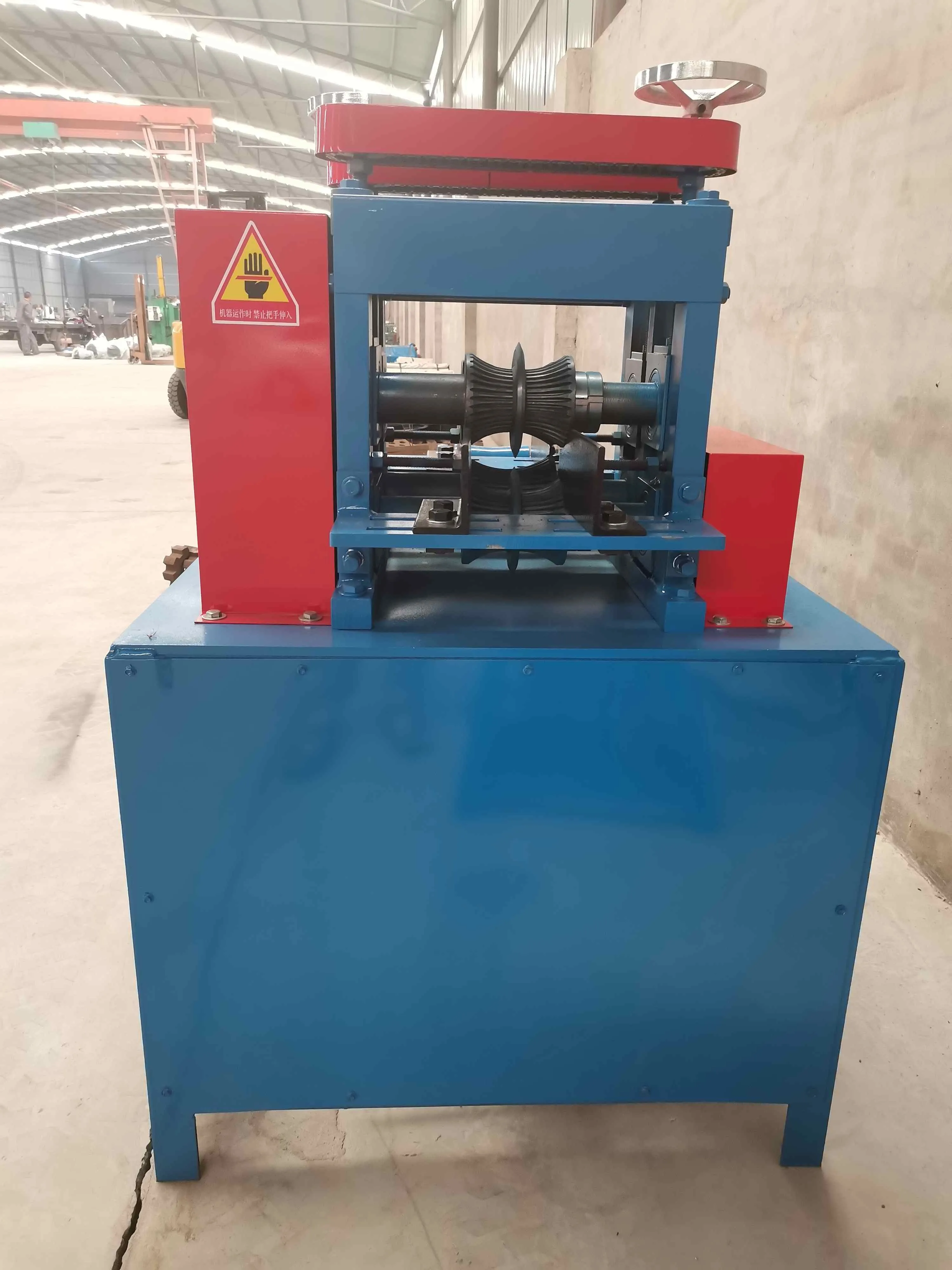
Initially, upon arrival, mixed recyclables undergo a primary sorting process. Large items are removed manually or mechanically to avoid machinery blockage. Heavily reliant on advanced technology, these plants feature conveyor belts equipped with sophisticated sensors and sorting machines that kickstart the sorting process.
Magnets play an essential role in extracting ferrous metals like iron and steel from the waste stream. Given their magnetic properties, these metals are easily separated using powerful overhead magnets or magnetic drums. This initial segregation is crucial, as it sets the stage for more specialized sorting required for non-ferrous metals.
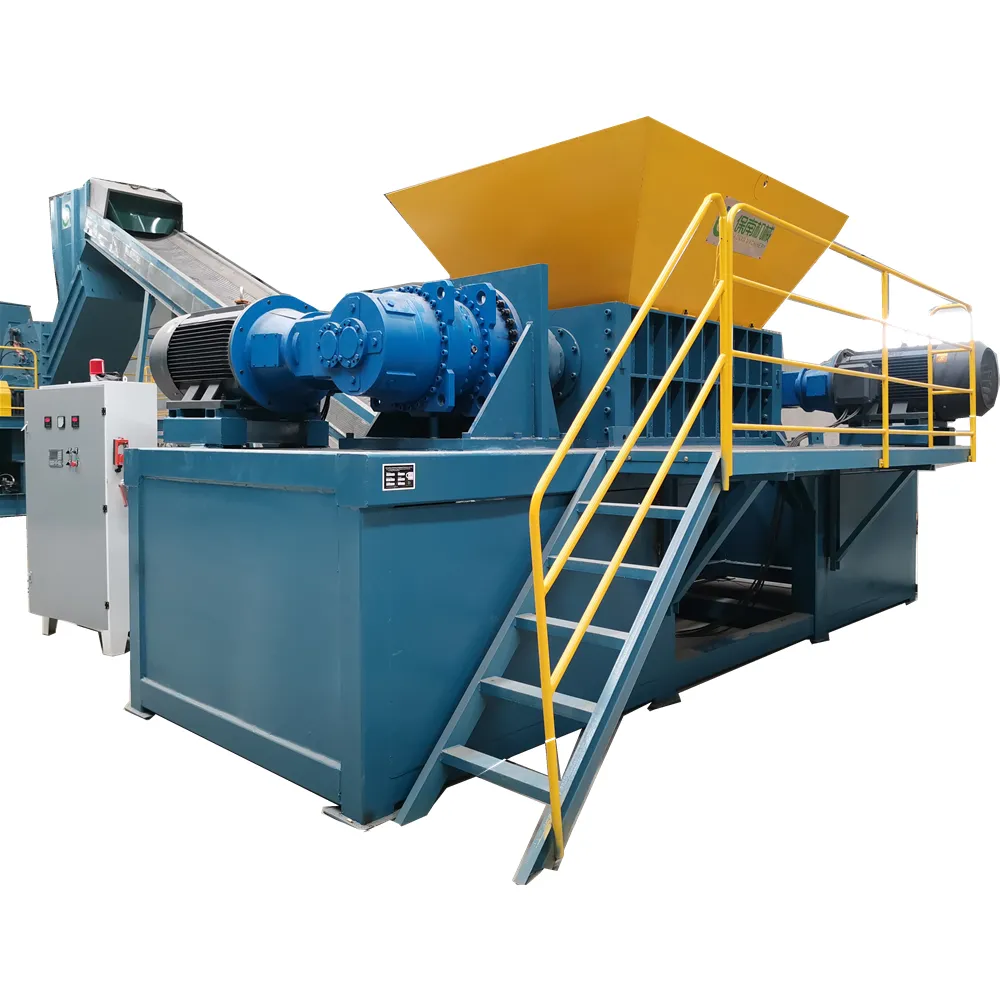
Non-ferrous metals—such as aluminum, copper, and brass—pose a greater challenge due to their non-magnetic nature. This is where Eddy Current Separators come into play. These sophisticated machines create a powerful magnetic field that induces currents in non-ferrous metals, causing them to be repelled and separated from other materials. By leveraging the principles of electromagnetism, recycling plants effectively sort out valuable aluminum from the rest.
Further refinement then ensues through advanced sensory-driven sorting systems. These incorporate cutting-edge technology such as X-ray fluorescence (XRF) and near-infrared (NIR) spectroscopy. Each method utilizes different principles to identify materials based on their fundamental properties. XRF, for instance, analyzes the elemental composition, while NIR spectroscopy relies on the unique light absorption characteristics of different metals. These sophisticated technologies ensure precise separation, even when dealing with mixed metals or complex alloys.
how are metals sorted in recycling plants
Beyond optical and magnetic sorting, the human element remains vital. Skilled operators oversee the process, identifying anomalies or non-recyclable elements that might slip through the automated screening. Their expertise provides an additional layer of quality control, ensuring the final output is of the highest purity.
Moreover, the commitment to sustainability extends beyond the sorting floor. Innovations in energy use, such as utilizing solar panels or optimizing machinery for energy efficiency, have become widespread across recycling plants. This not only cuts operational costs but also reinforces a commitment to an environmentally sustainable future.
As metals complete their sorting journey, they are compacted and prepared for reentry into the production cycle. The economic and environmental benefits are substantial. Recycling metals saves significant amounts of energy compared to mining raw ore, reduces greenhouse gas emissions, and conserves valuable natural resources.
The leadership and transparency of recycling plants bolster trust with stakeholders and communities. By actively engaging with educational initiatives, hosting facility tours, and publicly sharing data on their ecological impact, plants build public confidence and awareness.
In summation, the elaborate processes within recycling plants highlight a convergence of expertise in engineering, environmental science, and operational management. This dedication to meticulous metal sorting reflects a broader commitment to sustainable development. Such operations are instrumental in paving the way toward a circular economy, where waste is minimized, resources are optimized, and environmental impact is mitigated. This narrative underscores the authority of modern recycling methods not just in waste management, but in forging a sustainable future.