The realm of non-destructive testing has been revolutionized by the application of eddy current techniques, especially when it comes to assessing aluminum materials. This technology's unique ability to detect superficial imperfections and hidden discontinuities without causing damage has proven indispensable for industries relying on the integrity of aluminum components, such as aerospace, automotive, and construction.
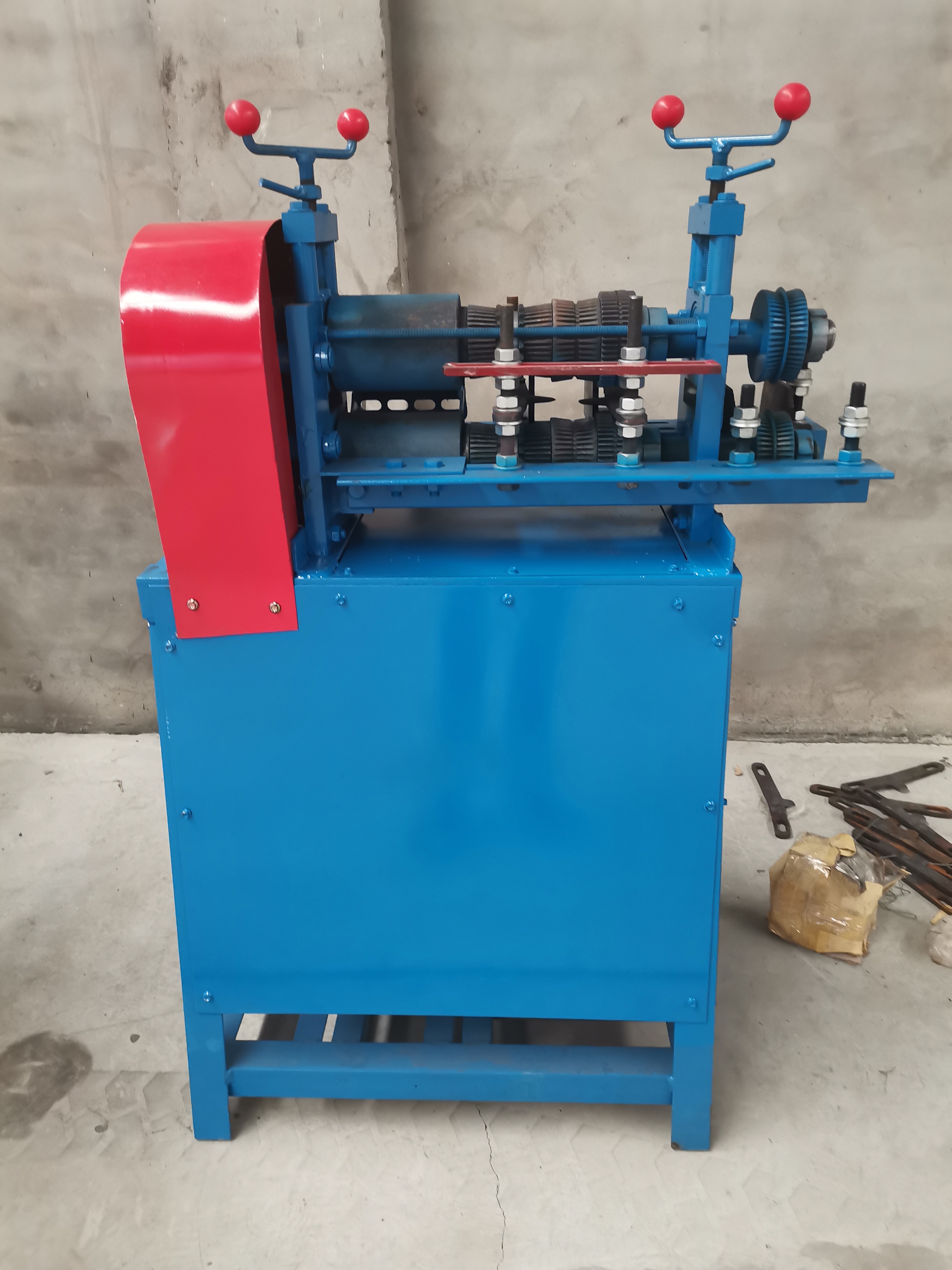
Eddy current testing, or ECT, leverages electromagnetic induction to identify flaws. When a probe containing a coil carrying alternating current is placed close to an aluminum surface, it induces swirling currents, known as eddy currents, in the metal. The flow of these currents is affected by the presence of discontinuities or variations in conductivity and permeability, which can be detected and analyzed through changes in the impedance of the probe coil.
Experience in dealing with aluminum through ECT reveals that the material's non-ferrous nature provides high sensitivity to surface and near-surface defects, which can be crucial for quality assurance processes. Specialists in the field of eddy current inspections stress the importance of a clean surface and a proficient technician to maximize detection capability. Ensuring that aluminum surfaces are free of contaminants is fundamental, as even minor residues can affect the outcomes of a test.
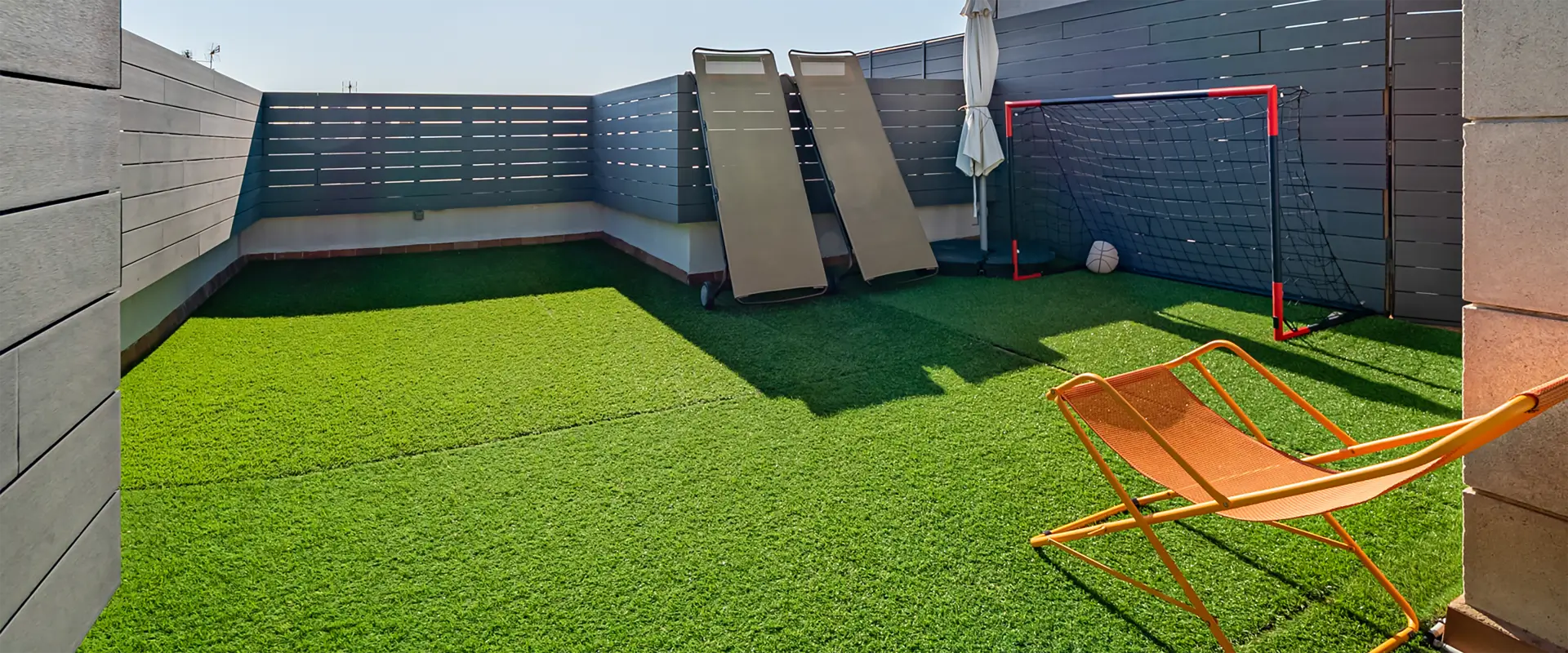
From an expertise angle, aluminum's conductive properties make it ideal for ECT, but understanding the signal interpretation and calibration process is key to successful implementation. Various factors, such as probe frequency and lift-off distance, must be meticulously controlled to enhance the signal-to-noise ratio. Knowledgeable practitioners will typically select lower-frequency probes for thicker sections of aluminum to penetrate deeper, while higher frequencies are reserved for detecting fine surface flaws.
eddy current aluminum
Moreover, the authority of ECT in the aluminum sector is bolstered by its versatility across different forms and conditions of aluminum products. Whether it be raw sheets, extruded components, or welded assemblies, ECT provides reliable detection of cracks, corrosion, and inclusions. There has been a shift towards automating ECT processes to increase throughput and repeatability in production lines, signifying trust in its efficacy and promoting uniformity across batch tests.
The trustworthiness of ECT as a diagnostic tool is reinforced by its compliance with international standards such as ASTM E215 for aluminum tubes and E1004 for conductive coatings. Adherence to these standards ensures a benchmark for inspection quality, breeds confidence amongst engineers, and assures end-users about the reliability of test results.
Organizations seeking to capitalize on the benefits of eddy current testing for aluminum are encouraged to integrate ongoing training for technicians and maintain their equipment rigorously. Partnering with leading practitioners and technology providers helps maintain an edge over competitors, ensuring product integrity and meeting safety standards. By adopting these practices, companies can depend on eddy current testing not just as a flaw detection method, but as a cornerstone of their quality assurance strategy.