Understanding the Mechanism of a Granulator
A granulator is an essential piece of equipment in industries that require the transformation of bulk materials into smaller, more manageable granules. This process is crucial for improving material handling, enhancing product consistency, and ensuring efficient mixing. In this article, we will delve into the working principles of a granulator, illustrating how it converts large particles into uniform granules.
At its core, a granulator operates based on the principle of pressure agglomeration. It consists of a large drum or container, equipped with a motor that rotates the drum at a controlled speed. The interior of the granulator is lined with a series of baffles, screens, or blades that are specifically designed to exert physical force on the materials placed inside.
The process begins as raw materials are fed into the granulator. As the drum rotates, the materials are lifted by the internal structures and then allowed to fall or are forced through screens. This action causes the particles to collide with each other and with the machine's surfaces, applying pressure that results in the breakdown of larger clumps into more finely divided pieces.
Simultaneously, a binding agent may be introduced. This liquid binder coats the particles, promoting adhesion between them upon impact This liquid binder coats the particles, promoting adhesion between them upon impact
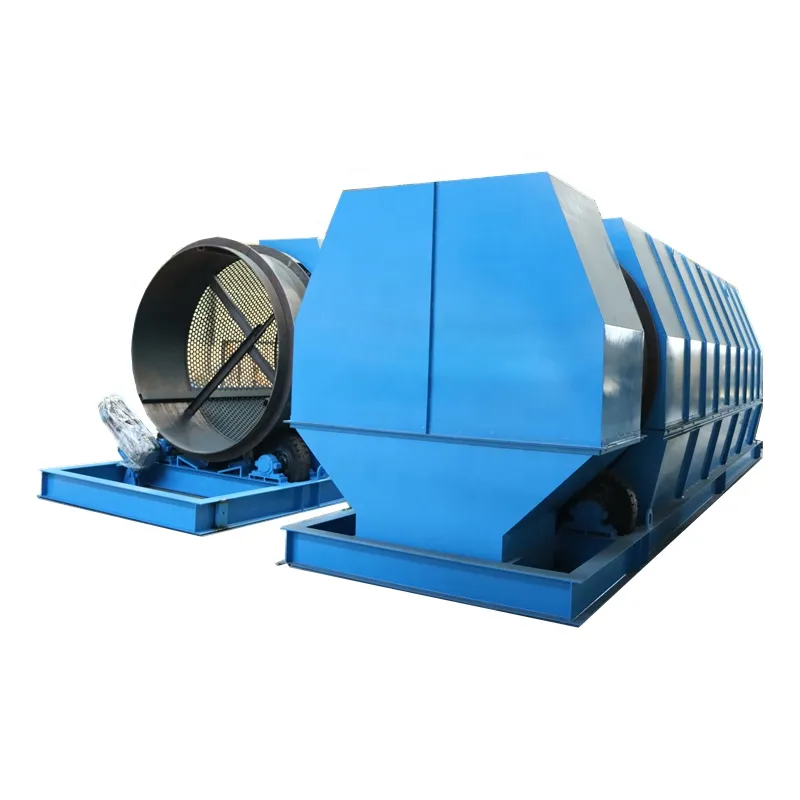
This liquid binder coats the particles, promoting adhesion between them upon impact This liquid binder coats the particles, promoting adhesion between them upon impact
how does a granulator work. The combination of pressure and binding agent leads to the formation of consistent, spherical granules. The size of these granules can be regulated by adjusting the screen mesh size or the rotational speed of the drum.
Throughout the granulation process, oversized granules are continuously broken down while smaller particles are combined, achieving a homogeneous product. This methodical approach ensures that the end product meets specific size and shape requirements, which is vital for various applications ranging from pharmaceuticals to fertilizers.
In addition to its primary function, a granulator also serves to improve material flow characteristics and reduce dust, thereby enhancing workplace safety and environmental conditions. The final granules are easier to store, transport, and use, making the granulator an indispensable piece of machinery in many manufacturing processes.
In conclusion, a granulator works by combining mechanical pressure with optional binding agents to convert bulk materials into uniform granules. Its operation hinges on precise control of rotational speed, screen size, and the addition of binding agents. The result is a product that is not only consistent in size but also superior in quality, setting the stage for further processing or direct use in various industries.