The Art of Precision An Insight into Metal Shredder Manufacturing
In the realm of industrial processing and waste management, the role of a metal shredder manufacturer is paramount. These specialized companies are the architects of machines that transform vast amounts of scrap metal into reusable resources, contributing significantly to the circular economy. A metal shredder manufacturer is not just a producer of equipment; they are innovators, engineers, and problem solvers, dedicated to enhancing efficiency and sustainability in the metal recycling industry.
The process of manufacturing a metal shredder begins with an understanding of the client's specific requirements. Each shredder is designed to handle different types and sizes of metals, from aluminum cans to massive steel beams. Therefore, the initial phase involves detailed consultations to determine the ideal machine configuration - whether it's a single-shaft, two-shaft, or four-shaft shredder.
Once the design blueprint is finalized, the manufacturing process commences. High-strength steels and robust alloys are meticulously selected for their durability and resistance to wear, ensuring the shredders can withstand the intense forces exerted during operation. Advanced CNC machines are employed to cut and shape the components with precision, guaranteeing a tight fit and optimal performance.
The heart of any metal shredder is its cutting system. A metal shredder manufacturer invests heavily in researching and developing these systems, often incorporating patented technologies. The cutting knives, made from specialized wear-resistant materials, are designed to fracture and reduce metal waste into smaller, more manageable pieces The cutting knives, made from specialized wear-resistant materials, are designed to fracture and reduce metal waste into smaller, more manageable pieces
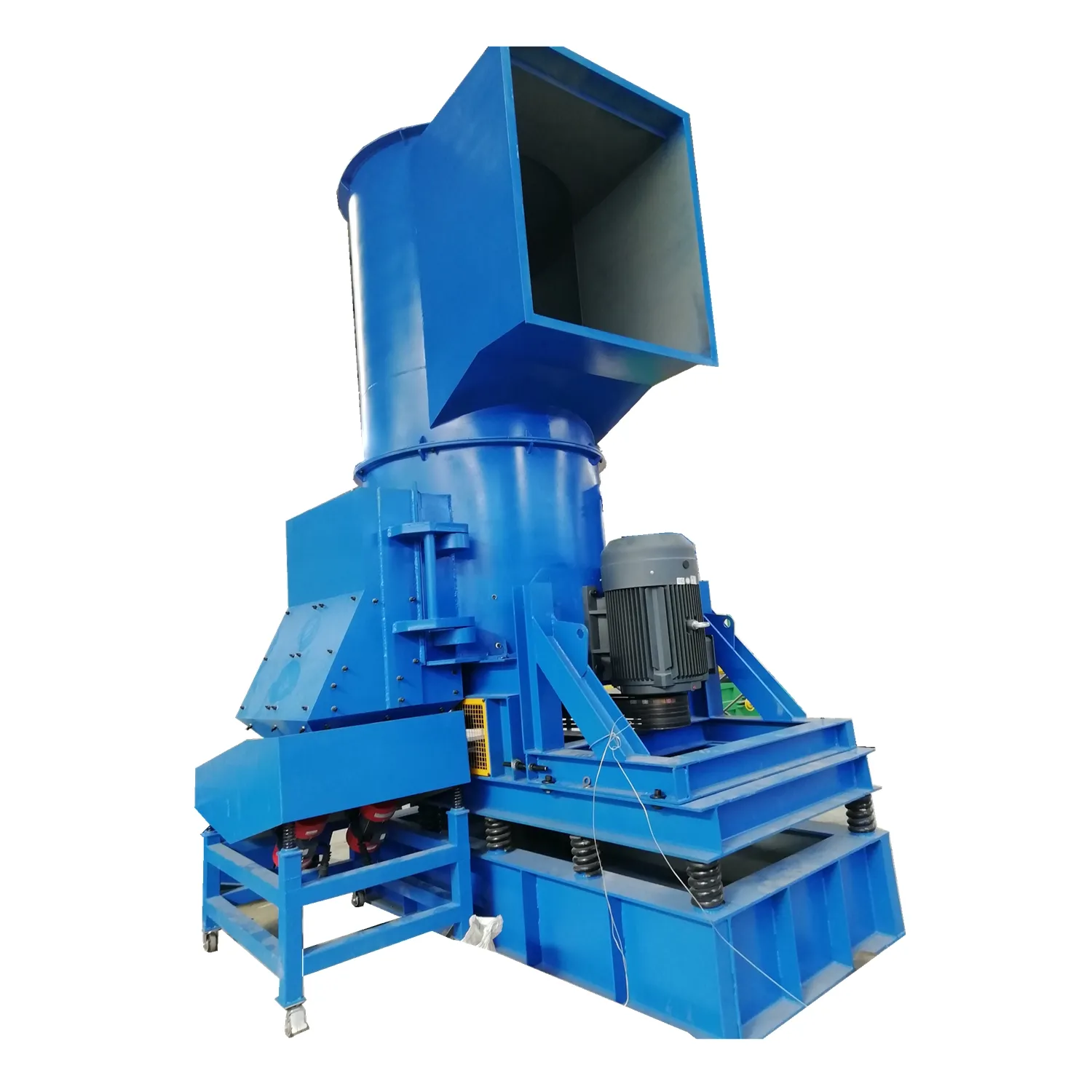
The cutting knives, made from specialized wear-resistant materials, are designed to fracture and reduce metal waste into smaller, more manageable pieces The cutting knives, made from specialized wear-resistant materials, are designed to fracture and reduce metal waste into smaller, more manageable pieces
metal shredder manufacturer. The intricate design and placement of these knives are crucial for efficient shredding and minimal maintenance.
Quality control is another critical aspect of metal shredder manufacturing. Each component undergoes rigorous testing before assembly, ensuring they meet stringent safety and performance standards. Once assembled, the entire shredder is tested under simulated operating conditions to verify its effectiveness and reliability.
Beyond the physical construction, a metal shredder manufacturer also focuses on technological advancements. Integration of automation, IoT sensors, and advanced control systems allows for real-time monitoring, predictive maintenance, and improved operational efficiency. This fusion of traditional manufacturing with digital innovation underscores the commitment to providing cutting-edge solutions.
In conclusion, a metal shredder manufacturer plays a pivotal role in the recycling industry, transforming waste into valuable resources while driving sustainable practices. Their dedication to precision engineering, continuous innovation, and customer-centric approach ensures that these machines remain at the forefront of metal waste management. As the world continues to grapple with resource scarcity and environmental challenges, the importance of metal shredder manufacturers in fostering a circular economy cannot be overstated.