The Aluminum Eddy Current An Innovation in Non-Destructive Testing
In the realm of non-destructive testing (NDT), the aluminium eddy current has emerged as a groundbreaking technology, providing engineers with a precise and reliable method for detecting flaws in metal structures. This innovative approach harnesses the principles of electromagnetism to identify discontinuities within aluminum components without compromising their integrity or function.
An eddy current is essentially an electrical current induced within conductive materials by an alternating magnetic field. When an aluminium component is exposed to such a field, it generates its own circulating currents. These currents are sensitive to any changes in the material's properties or structure, including cracks, voids, or variations in thickness. By analyzing the behavior of these eddy currents, technicians can accurately map the condition of the aluminum piece.
The application of aluminium eddy current technology offers several advantages over traditional NDT methods. Unlike techniques that rely on radiation or mechanical stress, eddy current testing is non-invasive and does not require direct contact with the test object. This means that inspections can be performed quickly and repeatedly without fear of damaging the material being examined.
Furthermore, the technique is highly sensitive and can detect minute defects that might go unnoticed by other forms of inspection. This sensitivity is crucial for industries where structural integrity is paramount, such as aerospace and automotive manufacturing, where even minor defects could lead to catastrophic failures.
Despite its benefits, the use of aluminium eddy current technology also presents some challenges
Despite its benefits, the use of aluminium eddy current technology also presents some challenges
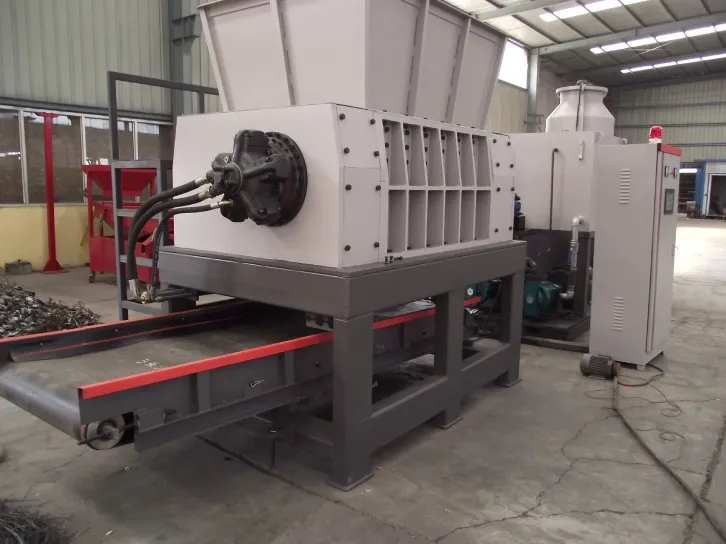
Despite its benefits, the use of aluminium eddy current technology also presents some challenges
Despite its benefits, the use of aluminium eddy current technology also presents some challenges
aluminium eddy current. For instance, the accuracy of the test can be influenced by factors such as the thickness of the aluminum, the distance between the probe and the surface, and the frequency of the applied magnetic field. Therefore, operators must have a deep understanding of both the equipment and the physical principles involved to ensure accurate and consistent results.
Another consideration is the cost and complexity of the equipment required for eddy current testing. High-quality instruments need to generate and detect precise magnetic fields, often requiring advanced electronics and sophisticated software for data interpretation. This may limit the accessibility of the technology to well-funded operations or specialized testing facilities.
In conclusion, the aluminium eddy current represents a significant advancement in the field of non-destructive testing. Its ability to provide fast, accurate, and non-invasive evaluations of aluminum components makes it invaluable across various sectors. As technology continues to evolve, we can expect further improvements in this area, leading to even more reliable and efficient inspection processes. Nonetheless, the expertise required to operate such systems ensures that the role of skilled technicians remains vital in harnessing the full potential of this exciting innovation.